Metal forging is the process by which metals are formed and shaped using compressive forces. Depending on temperature of the metal being worked upon, the process is classified into cold, warm and hot forging. Many automotive parts are forged due to unique advantages which include increased strength, different size/shape and mass production.
A typical forging press involves the moving vertical ram, die casts, bolster plate, ejector and frame. The vertical rams apply gradual and controlled pressure to the die holding a heated metal workpiece, causing it to take the shape of the die cavity. Due to the extreme pressure and shock loads involved in the process, the type and quality of lubricant used affects performance of these ram-based vertical presses.
Incorrect lubricant selection and inconsistent lubrication can reduce bearing life and lead to performance issues, including:
- Slow movement of the ram resulting in improper component accuracy
- Wear of the phosphor bronze bush bearings used in connecting rod, brake and clutch
- Excessive lubricant consumption due to frequent pumping
- Grease leakage from bearings resulting in fire hazard incidents
- Entry of forging dust and scale particles inside the bearings accelerating wear
- Sudden increase in operating temperatures of the bearing
- Chocking of distributors used in centralized lubrication system
The application requires special lubrication requirements. BECHEM provides best in class, special greases for forging presses with the following advantages:
- Longer life span of bearings as a result excellent wear protection with BECHEM’s range of greases. Customers have experienced bearing life of over five years with BECHEM Premium
- Resists bearing pitting: The special greases for the application create a high-pressure resistant film a result of the special additive package in the formulation.
- Strong adhesive property of the grease due to special tackiness improvers ensure a consistent lubrication film in the contact zone of eccentric shafts and phosphor bronze bearings
- Proven thickener and base oil combination for effective sealing of bearings to prevent external contamination.
- Prevent choking: Uniform and homogeneous structure of grease ensures no choking or clogging of distributors and tubing even if the machine is not in use for few days.
- Reduces grease leakage to ensure cleaner workplace as well as eliminate incidents of fire hazard.
The below case study illustrates how customized lubrication solutions for the hot forging press enhanced production efficiency at a renowned automotive component manufacturing brand.
Customer: A leading automotive components manufacturer in the world supplying a wide range of automotive components (such as distributor, gibs, connecting rod, brake and clutch journal etc), catering to both domestic and international markets.
The customer was using an extreme pressure grease of a popular brand “X” which was applied through pneumatic lubrication pump. The ‘On’ time for the pump was set 50 seconds.
Challenges experienced by the Maintenance team:
- Slow movement of ram in the mechanical system observed
- Sudden and abnormal rise of temperature in bearings.
- Severe grease leakage leading to higher grease consumption and fire hazard incidents
- During long idle hours, the issue of ‘distributor chocking’ was noticed.
- The removal of old grease from the equipment was a strenuous process.
The hot forging machine with a capacity of 2500, Tons has in-built temperature sensors, a modern grease pump and distribution system in place.
- Component name: Tripod Joint
- Number of strokes – 13 strokes/min
- Lubrication cycle- once in 100 strokes
- No. of strokes per Job- 3 strokes
- No. of stokes per Minute – 18 strokes
- Grease consumption per day – 21 Kg. /24hrs
- Monthly grease consumption: 504 Kg.
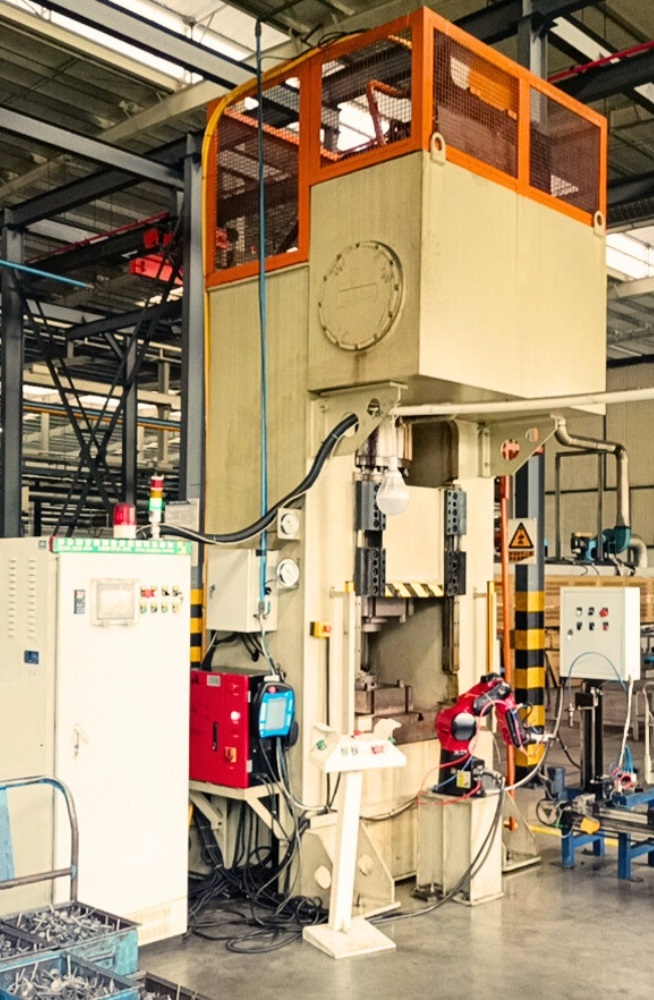
By considering the operational parameters and challenges, the BECHEM Application Engineering team recommended the high-performance grease “BECHEM Premium” for a trial.
Observations made during the trial period:
Trial period : 60 days
- Normal movement of the ram was noticed throughout the trial period.
- The re-lubrication cycle extended to 125 strokes in 30 Seconds.
- The issue of grease dripping was minimized.
- Operating temperature of the bearings were stable and sustained.
- Grease consumption reduced by 46.5% resulting in reduced operational costs.
- Issue of grease leakage was minimized reducing the risk of fire hazards.
- Process of degreasing was much easier.
Why ‘BECHEM Premium’?
- Developed with high quality base oil with optimum viscosity (110 Cst at 40˚ C), ‘BECHEM Premium’ ensures the formation of a high-load absorbent film.
- Fortified with special tackifier, ‘BECHEM Premium’ resists the ‘squeeze out’ phenomenon of grease from the bearings
- The grease being highly tacky in nature helps in providing a secondary function of efficient sealing for the bearing
- The special additive package in the formulation of BECHEM Premium ensures a high-pressure-resistant film that absorbs shock loads and prevents bearing pitting
- BECHEM Premium provides strong protection against corrosion, this is validated by the EMCOR test result rating of 0/0.
- Developed with an ultra-refined base oil of higher oxidative stability, ‘BECHEM Premium’ prevents clogging or drying out in the tubes and distributors even during long idling hours of the machine
- BECHEM premium is fully compatible with phosphor bronze bearings for wear and corrosion protection as these bearings operate in high temperature and humid environments
- Readily pumpable from centralized lubrication system.
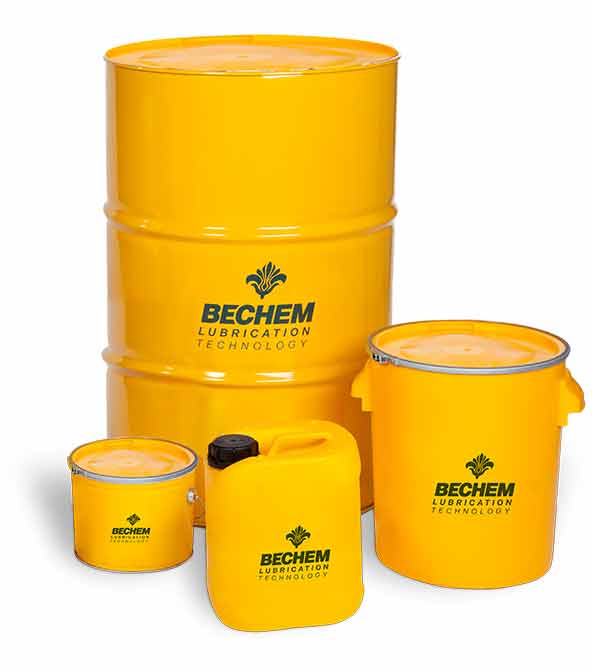
Observing the efficiency of ‘BECHEM Premium’ in optimizing production processes and minimizing maintenance costs during the trial, the customer switched over to BECHEM Premium for the rest of the presses.
*** pitting: Damage that is caused by the entry of foreign materials like dirt or other metal particles.
** EMCOR test evaluates the effectiveness of grease in preventing corrosion in roller bearings operating in water, saline water, and sodium chloride solution.
For more details on BECHEM Premium sample of the product, write to us at [email protected]
Support response: Median email response time of less than 3 hours.
Latest Blogs Updates
Impact of high performance forming oil on metal shaving process
Performance Case study of special forming oil, Beruform MF 155 C in metal shaving operation and positive impact on rejection rates. Metal shaving is a finishing operation in which burrs…
High Performance Grease for Effective Lubrication of Forging Press
Metal forging is the process by which metals are formed and shaped using compressive forces. Depending on temperature of the metal being worked upon, the process is classified into cold,…
How can dry film lubricants affect performance of automotive components?
Anti-friction coatings also known as solid-film or dry-film lubricants are recommended for applications where extreme operating conditions of very high or low temperatures and significantly high pressures are prevalent. Within…
Plastic Lubricants from BECHEM
Auto manufacturers have effectively been able to address the issues of design, energy efficiency, user comfort, aesthetic appeal, engineering flexibility and durability in interior cabins of the car by use…