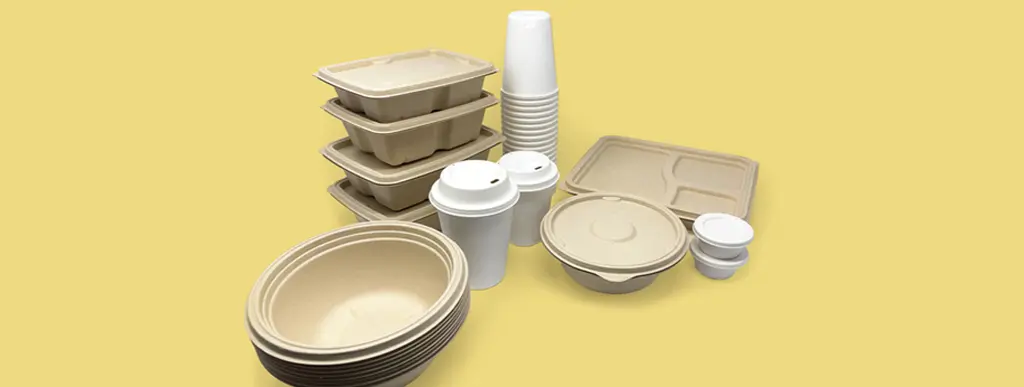
Machine, machinery components and effective cleaning
November 4, 2024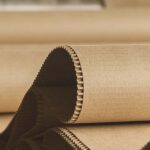
Enhance Corrugated mill reliability with high-temperature grease solutions
March 14, 2025Effective lubrication of pellet feed mill bearings
While the straight up grease cost is an important consideration, maintenance engineers recognize the importance of high quality lubricants and correct lubrication practices for effective plant maintenance and a reliable process. Factors such as grease consumption, replacement of spares, production downtime, manpower for re-lubrication exercise etc. can impact process parameters and reduce long-term expenses. This holistic approach not only enhances lifespan and reliability of machinery but also contributes to overall productivity and cost-effective operations.
Why consider high performance greases in animal feed pellet mills ?
The feed mill is a fully mechanized process and bearings play a key role. Besides enabling the grinding and pelleting of feed ingredients, bearings support the rotating shafts in feed mixers. However, during pellet production these pelletizing machines operate under extreme conditions including high temperature, pressure, water vapor and contaminants, which can impact bearing performance and consequently, the process efficiency.
Also the method of grease application, amount of grease applied can affect functionality of the roller bearings. For example over lubrication bearings can result in grease leakage and risk of feed contamination.
Regular lubricants and challenges for effective lubrication of bearings in pellet presses
- The bearing press typically operate at high temperatures (90-100˚C). Continuous exposure to such high temperatures can impact health of the grease film in bearings leading to metal-to-metal contact and wear
- Base oil evaporation and subsequent grease loss from bearings often accelerate grease consumption
- With regular greases, prolonged exposure to high temperatures can lead to buildup of solid residues of thickener in the bearings that can obstruct fresh grease flow and starve the friction zones
- In addition to high temperatures, moisture condensation during idle time can also lead to corrosion of the bearings
- Hence, the lubricant needs to form a protective shield against corrosion
- Equipment downtime during peak operations negatively impacts reduces productivity
Selection of grease with an appropriate formulation for pellet presses is critical to mitigate maintenance expenses and productivity losses. Grease suitable for bearings operating in extremely dusty and moist environments must offer effective sealing in addition to lubrication.
Customer : A leading Indian manufacturer of pellet and crumble feed, with a production capacity exceeding 20 TPH, also operates poultry breeding farms and hatcheries. The fully automated, state-of-the-art facility is designed to meet extensive in-house requirements.
Operation conditions of the pellet press:
- No of machine -2
- Machine Type PM615XW
- Application- Main drive shaft of press roller bearings
- Bearing Type – Single row taper roller bearing no. 32220
- Bearing Speed- 540 RPM
- Operating temperature – 110˚ C
- Greasing method – Single line automatic lubrication system
- Grease flow time- 2 mins once for every 10 mins of idle time
- Quantity of grease flow – 6.81 grams in 2 mins
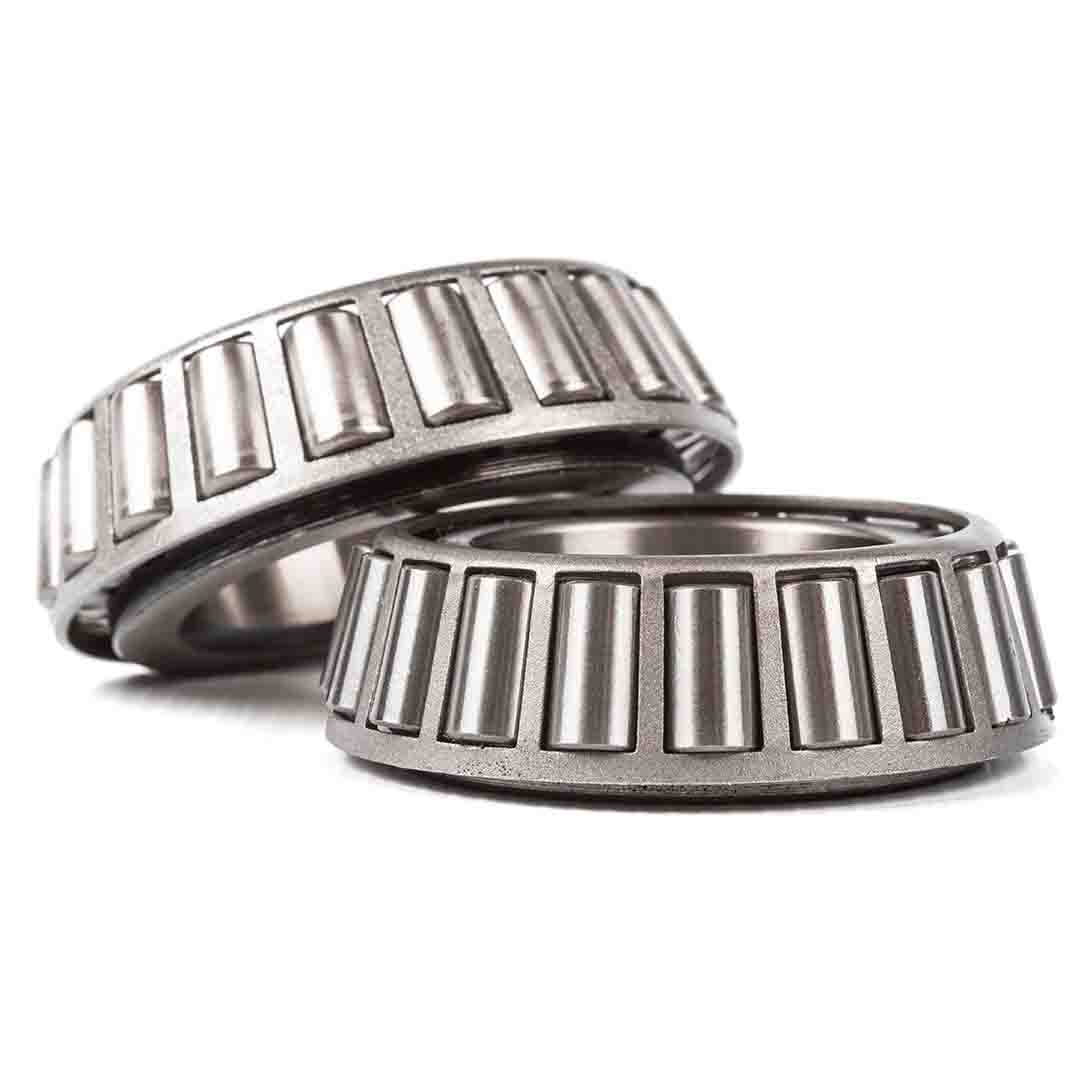
Issues faced by the customer:
- Due to the demanding operating conditions, lifespan of pellet roller bearings decreased to a maximum of three months, with multiple instances of premature bearing failures within a single month
- With process temperatures nearing 110˚ C approximately, cake like formation of grease was observed in bearings due to evaporation of base oil
- In order to avoid lubricant starvation, the grease pump was operated continuously resulting in higher consumption of grease
- With regular bearing failures, the unplanned equipment downtime to replace bearings in the rollers resulted in production loss
- Occasional mild contamination of oozed grease from the bearings with chicken feed led to batch rejections
Having assessed the above issues, the BECHEM team recommended the specially formulated polyurea thickened high temperature grease, Berutemp M2 KN, designed for superior performance of the pellet roller bearings.
Trial result :
- 40 % reduction in grease consumption
- No bearing failure during trial period
- Lifespan of bearings for pellet rollers doubled
- Eliminated grease leakage from bearings, reducing the risk of contamination and batch rejection
- No lump/cake formation of grease was observed at elevated process temperatures of 110˚ C
Sl.No | Process details | Brand ‘X’ | Berutemp M 2 KN |
1 | Grease flow time for every 10 minutes | 2 min | 1 min 10 sec |
2 | Total quantity of grease flow for every 10 min of idle pump time | 6.81 g. | 3.85 g. |
3 | No. of times Pump On / day | 121 | 130 |
4 | Total quantity of grease flow / day | 824 g. | 500.5 g. |
Why Berutemp M 2 KN?
- Longer service life: Inspite of exposure to process temperatures of over 110˚C, Berutemp M2 KN retained its consistency by preventing base oil oxidation and also ensured a resilient lubrication film on bearings
- Protection for bearings – Formulated with highly structured polyurea thickener with high shear stability, Berutemp M2 KN protects bearings from friction, wear for longer duration
- Excellent thermal stability – Based on high viscosity base oil of 490 cSt, Berutemp M2 KN remains stable and provides effective lubrication at high temperatures
- Prevents corrosion – Berutemp M2 KN protects bearings from corrosion and damage caused by moisture or water ingress
- Fortified with anti-wear additives and high viscous base oil, Berutemp M2 KN maintains lubrication effectiveness, preventing metal-to-metal contact and potential damage to bearings
After monitoring an extended two-month trial, no bearing failures were observed and substantial cost savings was achieved, the customer switched to Berutemp M2 KN.
For further details of the product, comparison chart and trial samples, write to us at [email protected]
Support response: Median email response time of less than 3 hours.