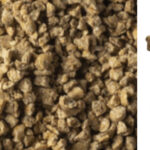
Effective lubrication of pellet feed mill bearings
March 13, 2025Enhance Corrugated mill reliability with high-temperature grease solutions
The corrugated sector, driven by e-commerce and sustainability, has experienced growing demand for containerboard as packing material.
The corrugated machine line is a versatile set-up designed to produce single, double or multiple plies of corrugated sheets with an assembly of rollers operating in tandem. Effective lubrication of roller bearings within the segments of single facers or double backer is critical for continuous operation of the line. A roller bearing failure within the segment can lead to significant equipment downtime and production loss.
The roller bearings within the segments operate under high speeds and considerable loads. Additionally, the heat roller bearings are subjected to high temperatures and steam as the rollers are pre-heated for quick drying and conditioning of the bonded liner and fluting sheets.
Effective lubrication of bearings would improve their operational reliability and productivity of the Corrugated machine. Additionally, lubricants that can provide longer service life will reduce the re-lubrication frequency and associated man-power costs.
4x increase in lubrication life with special poly urea grease, Berutox FH 28 EPK 2 at high temperature bearings of corrugator machine.
Customer: A renowned corrugated box manufacturer, equipped with fully automated production lines in a state-of-the-art facility. Having a monthly production capacity of more than 2500 MT supplies to FMCG sector.
Operational parameters:
Application area | Corrugating and pressure rolls of a fully automatic machine |
Bearing nos. | NU224 and NJ334 (mounted horizontally) |
Total no. of bearing | 12 nos. |
Operating temperature | around 180°C |
Bearing speed | 130 RPM |
Customer was using a lithium complex-based grease of brand ‘X’ of NLGI grade 2.
Key challenges:
Persistent grease leakage from the bearing housing, caused significant accumulation on the machine base, resulting in poor housekeeping. This required daily cleaning, increased lubricant consumption and higher maintenance costs. Additionally, the frequent need to replenish grease increased the man-machine interface affecting the safety quotient and also impacting production schedules.
BECHEM’s Recommendation:
High temperature grease, Berutox FH 28 EPK 2.
High performance grease formulated with poly urea thickener and synthetic base oil of high viscosity index.
Reason for Recommendation :
The grease offers excellent thermal ageing, shear stability and sealing properties.
It’s High viscosity index PAO base oil minimizes viscosity changes at high temperatures, ensuring a strong lubricating film.
Formulated with advanced additives Berutox FH 28 EPK 2 provides superior thermal stability, extended longevity and exceptional protection against wear and contamination in high temperature conditions.
Trial observations:
- No evidence of grease bleeding or leakage from the bearing housing was observed during the trial period of 5 weeks
- Re-greasing interval extended significantly from one week to five weeks
- Extended re-greasing frequency led to a substantial reduction in the quantity of grease consumption
Condition of used Berutox FH 28 EPK 2 after a span of 3 weeks.
Key benefits:
- Bearing protection: Fortified with anti-wear additives, Berutox FH 28 EPK 2 ensures longer service life of bearings by maintaining strong lubricating film that resists high temperatures and centrifugal forces.
- Enhanced operational efficiency: Seamless operations without frequent re-greasing procedures leading to improved productivity.
- Cost effectiveness: Substantial reduction in grease consumption led to significant cost savings over time.
Result:
Following the impressive results of the trial period, the customer switched to Berutox FH 28 EPK 2 high temperature grease for the other three machines in their plant.
For further details of the product, comparison chart and trial samples, write to us at sales@bechemindia.com
Support response: Median email response time of less than 3 hours.