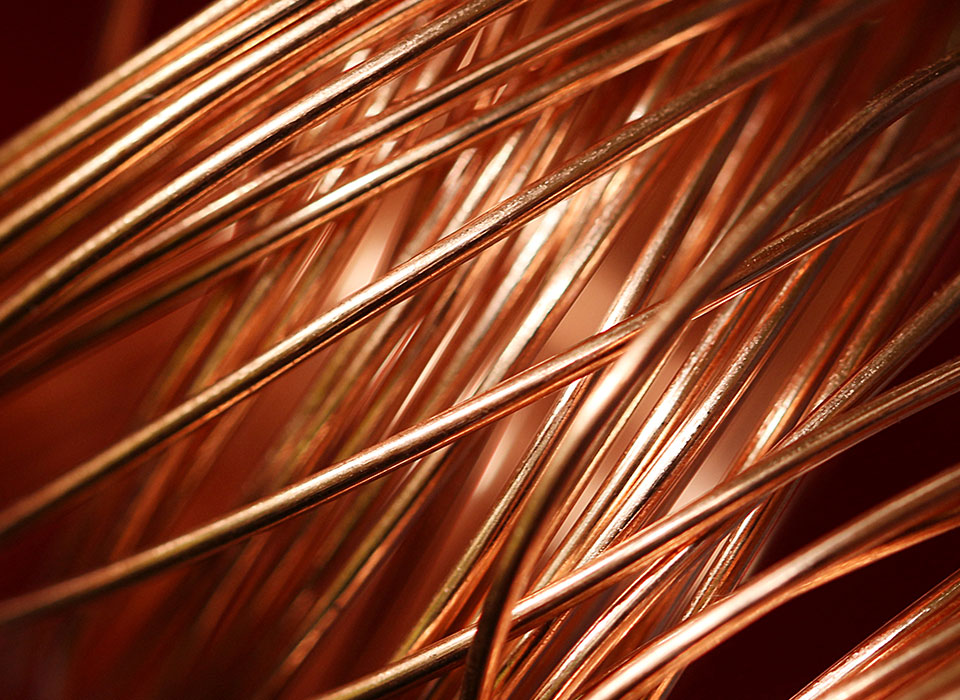
Copper dust affecting surface finish and rejection rates in copper wire drawing process
March 19, 2024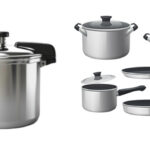
Effectiveness of metal forming oil in deep drawing operations
November 4, 2024Impact of high performance forming oil on metal shaving process
Performance Case study of special forming oil, Beruform MF 155 C in metal shaving operation and positive impact on rejection rates.
Metal shaving is a finishing operation in which burrs from the cut edges are sheared off in order to make the edges smooth and also impart dimensional accuracy. Shaving operation is typically preceded by punching, piercing or other stamping operations that further require close dimensional tolerances.
An effective lubricant will help in component finish and can also impact die life. Below case study demonstrates benefits of using a high performance lubricant over a conventional oil in an actual use case scenario.
Customer: A leading manufacturer of precision stamping parts for commercial vehicles, agricultural machinery and construction equipment. With more than 100 stamping machines of varying capacities, the company specializes in manufacturing brake part assemblies, chassis structures and blocks.
Application details:
Component : Brake-pad body
Material : Steel and mild steel
Thickness : 2-7 mm
Operation : Shaving (link to metal shaving within case study)
Customer was using a regular blanking oil with viscosity of 50 Cst at 40˚C.
Issues encountered by the operations team:
- Frequent maintenance or dressing of the shaving tool due to accelerated wear
- Reduction in die life, leading to increased production downtime
- Significant increase in material rejection rates. Material rejection was also reported from end customers as well.
Key challenges presented to the Bechem team:
The Operations team listed the below aspects as ‘improvement parameters’ against which performance of any trial lubricant would be measured,
- No cracks or fractures on the component
- The occurrence of burrs sticking to the die during the shaving process must be avoided
- Reduction of excessive heat buildup on die/machine and workpiece being processed
- Reduction in ‘burr’ component edges and enhanced surface finish
- Also minimize oil consumption
After analyzing the operation parameters and considering the expectations put forward, the BECHEM team recommended the high-performance cold forming oil, Beruform MF 155C.
The team identified, two 150 ton punching presses to conduct trials, one with single shaving and the other with double shaving operation.
Based on the success of a pilot lot, a rigorous 24-hour trial was carried out to evaluate the performance parameters.
Trial observations:
- Superior surface finish of the punched components without any signs of overheating
- Zero component rejection
- No signs of stickiness on the die or punch. Punched surfaces exhibited better finish
- Approximately 40% reduction in punched components. Operators could now hold the component with ease
- Continuous stamping operation for two shifts without interruption, indicated stability and reliability that could be achieved with Beruform MF 155 C.
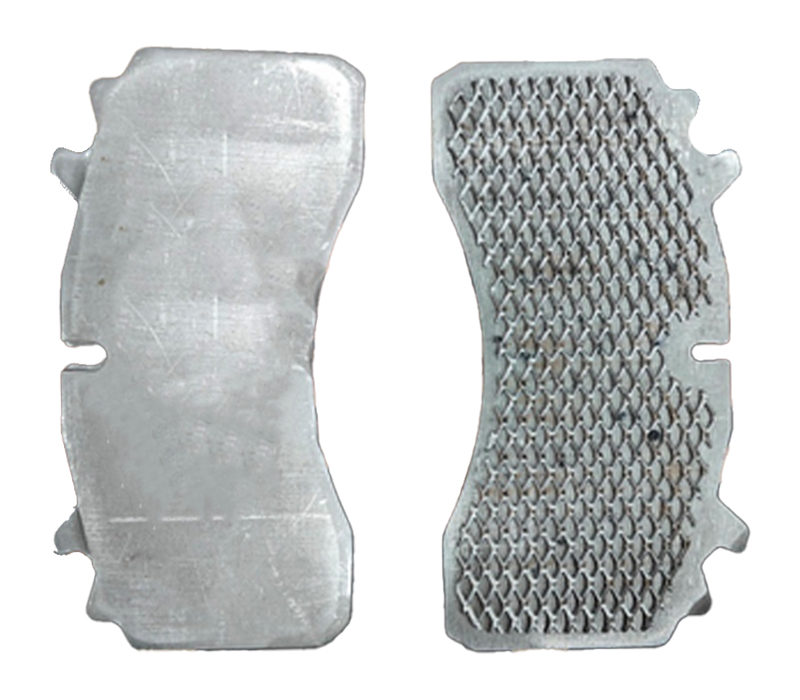
Result:
Post witnessing the exceptional performance with Beruform MF 155 C, the customer extended the trial for the next couple of months. It was observed that die life improved by 20% in comparison to the earlier blanking oil. Additionally, reduction in rejection rates and overall positive impact on production process was witnessed during this period. Consequently, the customer established Beruform MF 155 C as their ‘go-to’ forming oil for their processes.
For further details of the product, comparison chart and trial samples, write to us at [email protected]
Support response: Median email response time of less than 3 hours.