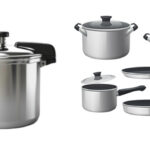
Effectiveness of metal forming oil in deep drawing operations
November 4, 2024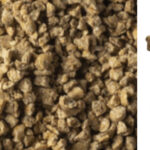
Effective lubrication of pellet feed mill bearings
March 13, 2025Machine, machinery components and effective cleaning
Performance report of Beruclean 3849 as an acidic cleaner
Manufacturing of paper and pulp-based utensils used in packaging and read to eat industry, involves liquid pulp filled into metal moulds of desired shape and cured at high temperatures. The sticky pulp with process chemicals leave residues on metal moulds typically made of steel and aluminium metallurgy. Even further, the pulp slurry clog the fine holes (dia) in the metal mesh, hindering the moulding process during continuous production runs.
Thorough and spotless cleaning is critical before reusing these moulds as it would impact finish of the final product. However, the pulp residues after the curing process are a pain to be cleaned. Also, rougher the process of cleaning, shorter the life expectancy of the moulds with intricate mesh. Abrasive cleaning methods can shorten the life of components, hence immersion cleaning with compatible cleaner is recommended.
Beruclean 3849
Beruclean 3849 is a liquid acidic cleaner specifically formulated for high-temperature environments and can effectively break down tough deposits on components and moulds. It is designed to address the unique cleaning challenges faced by paper tray manufacturers.
Best suited for manual, ultrasonic and spray cleaning methods.
Compatible with metals, ceramic glass, plastics and other acid resistant materials.
Removes organic and inorganic residues including tough lime deposits.
Below case study illustrates the effectiveness of Beruclean 3849 as a cleaning agent in the paper and molded fiber packaging industry
Customer : A renowned Indian manufacturer of paper and molded fiber food packaging products from compostable waste. The company with an installed capacity of more than 200,000 MT, operates fully integrated facilities with strong focus on quality and sustainability.
Cleaning concern with Mould Plates
- The customer was experiencing an issue to remove hard, sticky layer of dried, burnt pulp on the aluminium mould plates.
Cleaning concern with Mould Plate Mesh
During the moulding operation, woven wire mesh moulds are dipped into the pulp sump, where suction pressure shapes the wet pulp over the wire mesh. To maintain high suction pressure and precise mould formation, it’s crucial to keep the wire mesh free of holes free from blockages.
The Maintenance team had set-up a cleaning process in two phases to clean the double layer stainless steel mesh moulds.
- Frequent cleaning with high-pressure water spray method after every batch
- Intense cleaning of steel mesh moulds when removing them during equipment shutdown, fortnightly.
Inspite of the dual procedure, the customer was not satisfied with cleanliness of the mesh. Observing struggles of the Maintenance team, Bechem engineers recommended a trial with acidic industrial cleaner, Beruclean 3849.
Trial Procedure
- A sump was prepared with varying concentrations (3 and 5%) of Beruclean 3849 cleaner using 30 liters of water at room temperature.
- Mould plates were immersed in the cleaning solution for 30 to 45 minutes.
- The metal plates were then rinsed with regular water.
Component | Metallurgy | Concentration | Type of cleaning | Immersion Time |
Mould Plates | Aluminium | 3% | Immersion | 45 minutes |
Mould Plate Mesh | Stainless steel | 5% | Immersion | 45 Minutes |
Trial observations:
- Mould Plates
- Shiny clean surface of aluminum plates to the satisfaction of the Maintenance team was achieved
- Mould Plate Mesh
-
- 95% cleaning efficiency was achieved on the mould meshes
-
Before
After
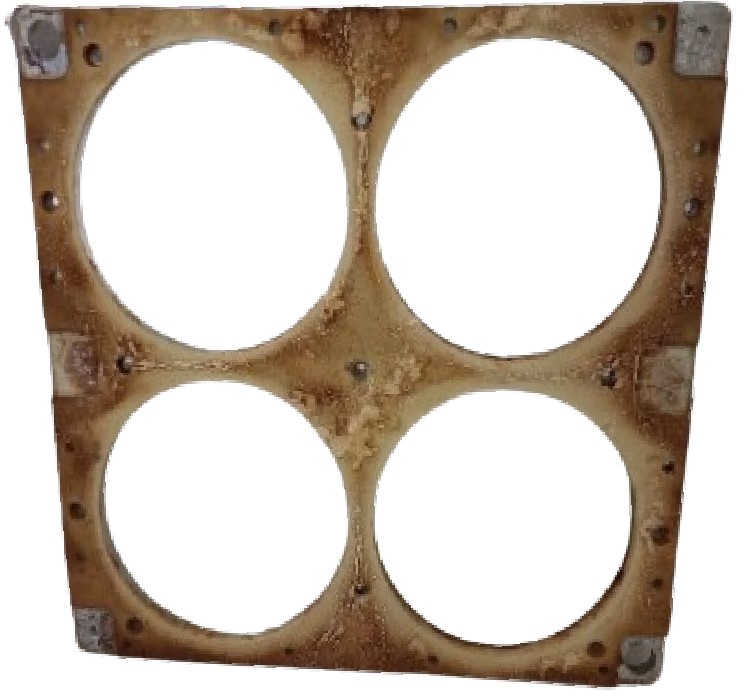
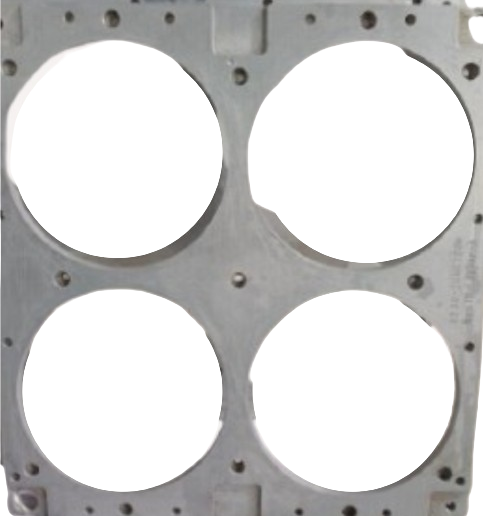
Result:
Having experienced the performance of Beruclean 3849 cleaner, the customer switched to Beruclean 3849 for all machine cleaning applications.
For further details of the product, comparison chart and trial samples, write to us at [email protected]